Motor Transfer Mechanism on the Side of the Belt Conveyor Examples of Miniaturization
Issue
Improving workability while reducing the protrusions on the side of the conveyor
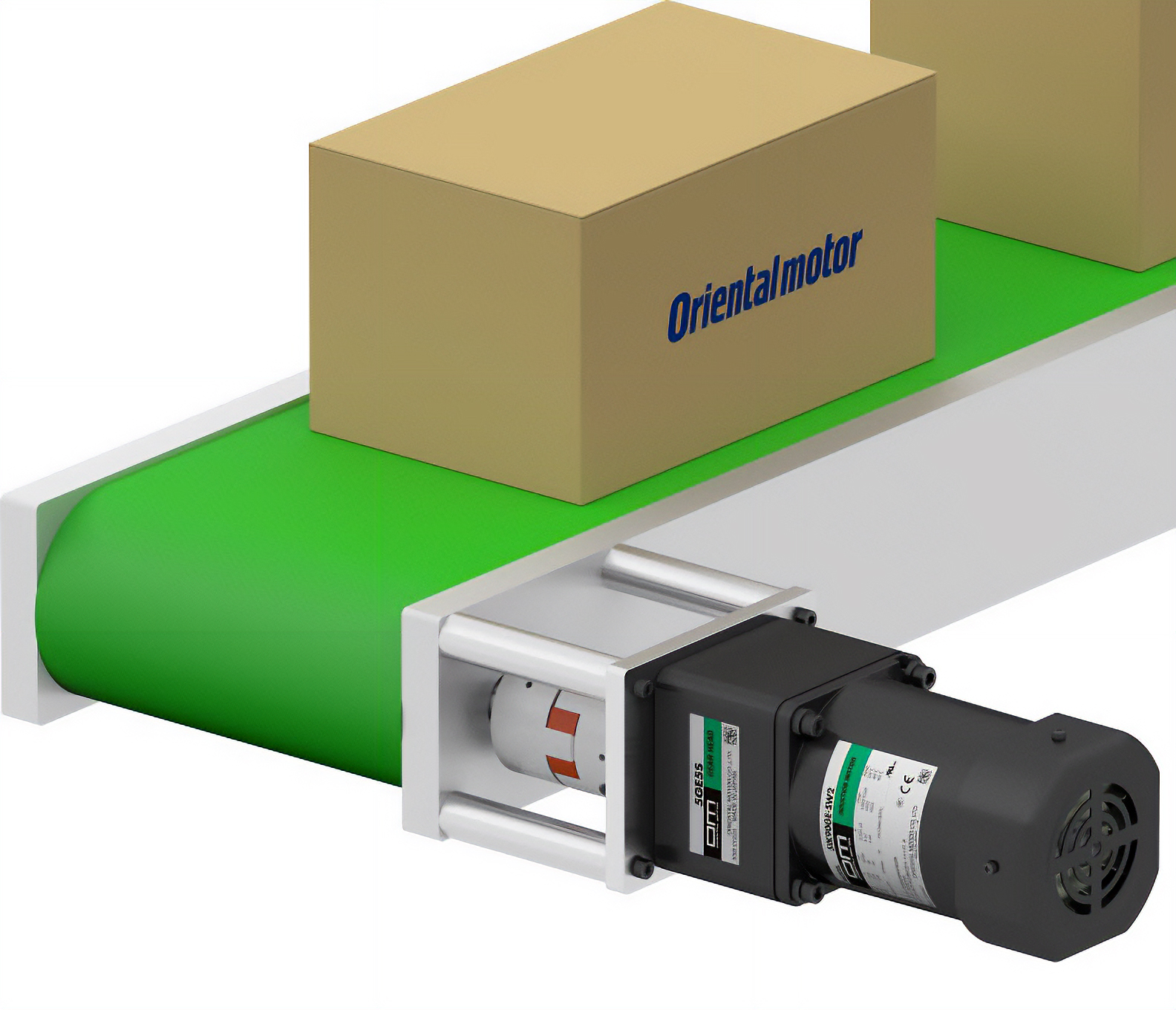
Conventional Equipment
Three-phase induction motors are coupled and driven by a coupling mechanism (an inverter is used for speed control)
- Application
- Transporting loads
Conventional Problems
- Motor, transfer mechanism, and other components protrude from the side of the conveyor, creating excess space
(The space occupied by each conveyor is large, making it difficult to add new equipment) - The number of parts to be installed in the equipment is large, increasing the overall assembly labor
Solution
Brushless Motor BMU Series
with JH gearheads (right-angle gearheads)
for conveyor space saving and work time reduction
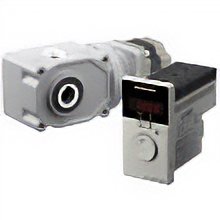
The use of JH gearheads (right-angle gearheads) in the BMU Series of compact, high power brushless motors reduces the protrusion of the motor on the side of the conveyor. In addition, the JH gearhead is a hollow hypoid, which reduces the number of parts needed to connect it to the conveyor.
This will also reduce the overall assembly labor, contributing to a reduction in work time.
Specific Application Examples
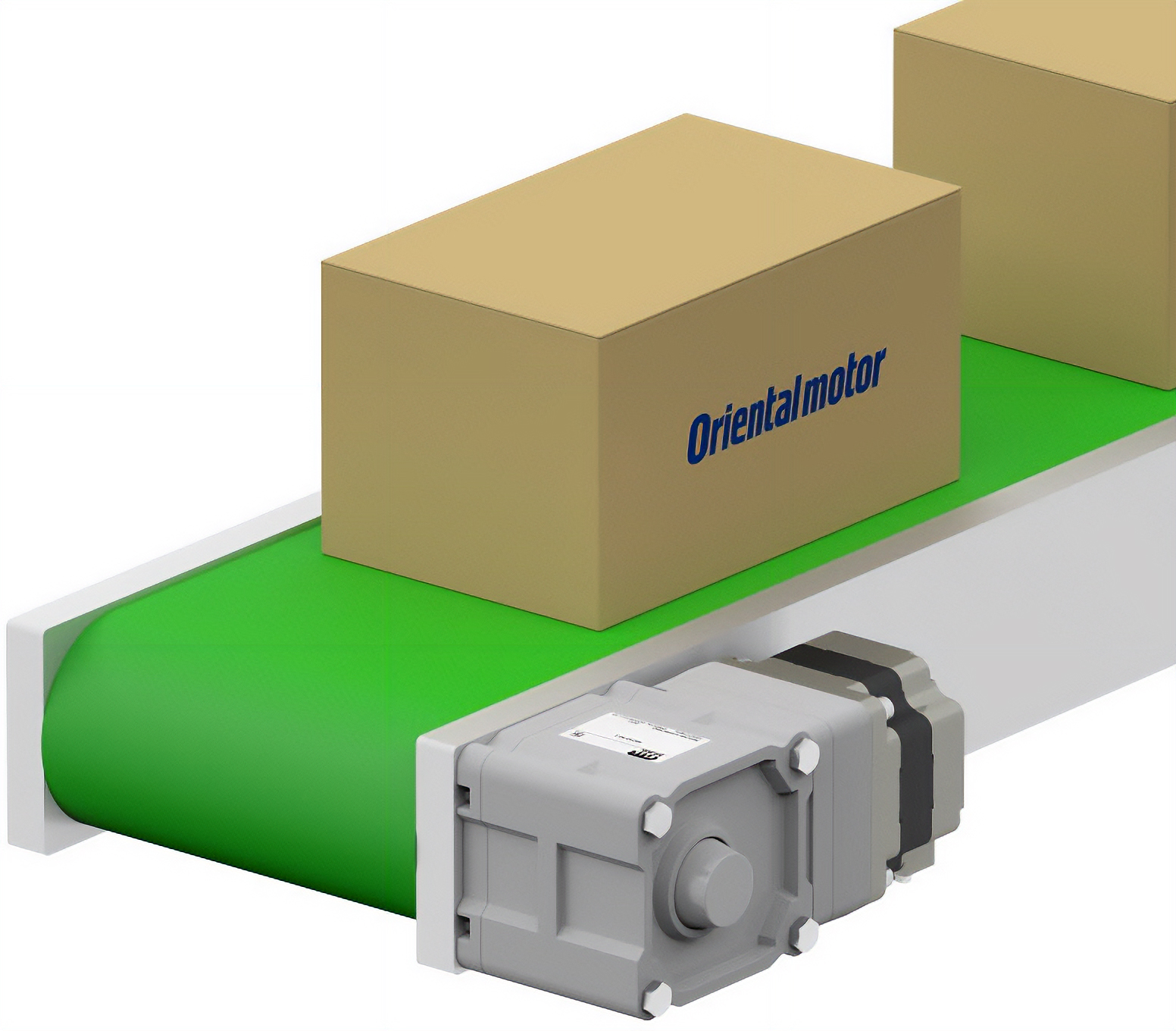
- Uses right-angle hollow shaft hypoid JH gearheads with high strength and high permissible torque
- Gearheads are directly connected to the belt conveyor shaft, contributing to space saving
- If you use a torque arm, you can fix it to the belt conveyor in one place
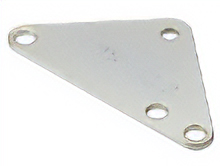
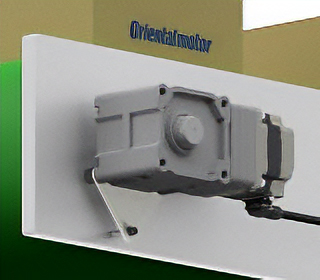
Reduction of the number of parts reduces the working time
By omitting the transfer mechanism, the time required for design and assembly, as well as for parts ordering and management, can be reduced.
Equipment Width and Height of the Conveyor | Number of Parts Required for Coupling | |
---|---|---|
Conventional Equipment | ![]() |
With mounting plate ×1 Couplings ×1 Spacer ×2 |
BMU Series JH Gearhead |
![]() |
![]() |